『导读』在德瑞博冲压车间共拥有冲压模具200套,拥有4台高精度机械压机和6台机器人,采用机械冲压机群,冲压精度高,生产效率高,平均6秒一次性冲压成型。
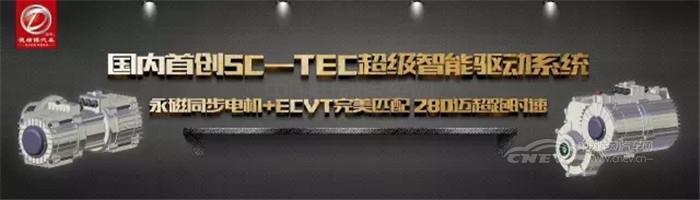
作为一款高品质纯电动SUV
德瑞博FW自上市以来备受追捧
如此高品质的表现
离不开德瑞博独步国内的独门“绝招”
这些绝招不仅仅局限在技术层面
还有它独有的平台优势
接下来
小编就带你探寻TA的高品质!

冲压车间是生产制造的第一个环节,冲压车间生产的关键是模具,它们是保证生产质量和精度的关键。经过冲压后制成车身主体侧围、车门、前机盖等部件。整个车间的机器化、自动化程度是同行业内最高的。
在德瑞博冲压车间共拥有冲压模具200套,拥有4台高精度机械压机和6台机器人,采用机械冲压机群,冲压精度高,生产效率高,平均6秒一次性冲压成型。

在焊装车间,整条生产线已实现完全自动化,平均每3分钟就有一台新车下线,在同行业内空前规模最大、最先进,生产技术规模化和智能化带给我们全新的视觉震撼。
在整车底盘的焊接流水线上,10台机器手臂同时在流水线上挥舞,据德瑞博工作人员介绍,单辆德瑞博产品车底盘有600多个焊接点,全部由机器人完成。这整套流程几乎不需要人工的介入,都是通过远程操控及智能机器操作内部设定完成的,他们能完成普通流水线更复杂的工艺技术,生产出来的每一台产品能节省人力和人为操作造成的偏差,保证了每一台产品的生产效率和工艺。

在涂装车间, 五彩缤纷的车身颜色及高品质的油漆效果是电动车给消费者的第一印象,也是仅次于电动汽车价格考量的第二要素,德瑞博车身采用无腻子式涂装工艺,由此可见涂装工艺处理技术的优越性,这也是德瑞博汽车面漆青靓丽出彩的精髓之一。
在涂装车间生产线上,为了确保最终每一辆产品的美观度和耐腐蚀性,每一件产品经过自动输送系统、从磷化前处理、电泳、清洗、脱水、烘干、固化 — 加热 — 静电喷粉、喷漆 — 检验 — 下件等多道工序,从而使产品确保稳定而符合标准的工艺状态和参数,平均每3分钟完成一辆车的喷涂全处理过程。
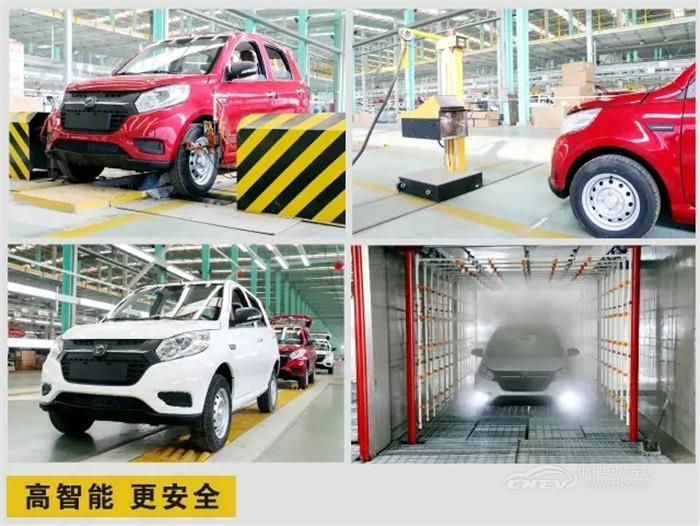
德瑞博汽车总装车间采用年产15万辆的总装线,拥有600米长的工艺装备,保证足够的工作空间,工人能以舒适愉悦的状态进行工作,从而保证生产的效率和质量,生产出品质最好的产品。
总装流水线采用ERP、同步供货和免检上料体系,确保上线零部件质量和物流成本,高精度动态整车参数检测线,确保产品调试精度和质量,德国博世电动工具,确保精准的扭矩和装配效率。
除了微型电动汽车一流的制造水平,让人颇感惊喜的是德瑞博汽车的检测系统。车辆在总装线完成所有的安装工作后,将驶入检测线进行下线前的质量考验,经过200多道工序检验,四轮定位自动检测、转鼓测试、声光监测、制动检测、速度检测、淋雨测试等检测项目,通过这些考验的车辆才能够进入外观检测区,检验员利用平行光源对车辆进行细致检查并通过比利时路、搓板路等综合路况进行路试的多重考验,最终成为一辆高品质的商品车。