『导读』这篇文章主要介绍新能源大巴的电池和BMS的结构与乘用车的区别,本文主要分三个部分,新能源大巴行业、新能源电池
第一部分 新能源大巴行业
其实数数全球的商用车(大巴+卡车),大致的方向还是沿着就有的习惯做HEV,国内总体而言,是以纯电动+PHEV为主的。这里的主要原因,还是欧美日在发动机和变速箱方面的积累,如果按照国内的纯电动大巴模式,配置300kwh以上的,很大的价值都给电池给占去了。
·商用巴士:New Flyer、Thomas、Navistar/IC、Volvo、Hino、Smith、GM、Daimler、TOYOTA和MitsubishiFuso。
·卡车 Smith、Volvo、Navistar、Daimler、TOYOTA、Hino、ISUZU、Iveco、PACCAR、Azure Dynamics、Daihatsu、Nissan和Mitsubishi Fuso。
图1和图2的数据制图,是参考了《Key Facts of the Power Battery Development in 2013:E-Motcycle & EV》一文里面的数据。
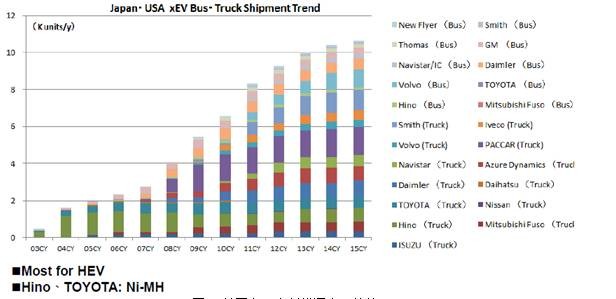
图1 美国和日本新能源大巴的情况
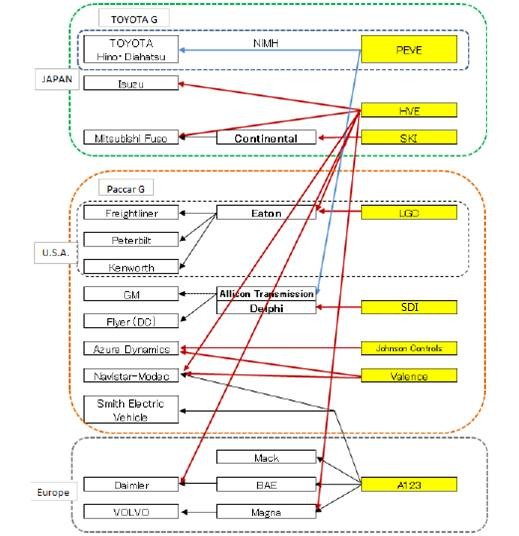
图2 除中国外新能源商用车电池供给情况
与之相比,国内的情况是根据补贴来的,有了较大的单位的每度电补贴以后,做纯电动这种形式就变得更有利了。所以总体来说,对于商用车的以每度电补贴,完全扭转了整个技术路线,直接把国内所有做大巴的企业将HEV砍掉(这事就是发生在2013和2014的时候,现在已经回不过去了),转到BEV和配置较高的电池的PHEV的形式上来了。
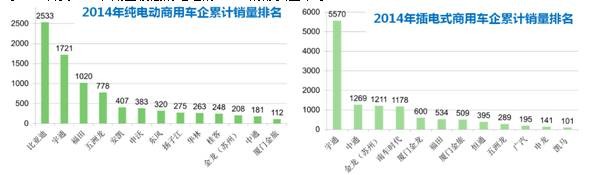
图 3 2014年中国商用车销售情况
更有趣的是,通过配置电池,将电动里程零耗油的部分换算进去,就可以把整个驱动系统的效率的差异打掉,所以对比国外的技术水平,我们的PHEV一下子把老师傅给超过去了。这个有点类似文字游戏,是通过加多了钱(国家补贴和地方补贴)配置多的电池的代价换来的。从运营公司的角度来看,用电还是省钱,所以出现某地一天充五次插电式大巴的故事发生了。
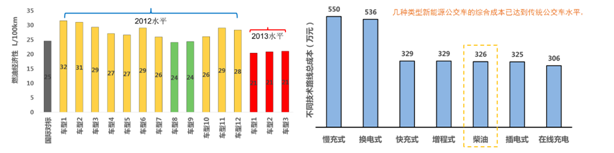
图4 商用车的油耗水平
第二部分 新能源大巴电池系统架构
我们这里使用A123&万向的例子来看这个系统架构,我们来对比两个案子美国的Navistar和上汽万向的纯电动大巴,他们都是拿着A123的模组来,按照A123的基本成组模式。
1) 上汽和万向合资纯电动大巴
图5包括模组成组,电池包布置还有系统框图,其中模组(含BMU)这一级,基本是电池厂出来各个产品(大车、小车)都能用了。整个从单体=》模组=》电池包,然后在车顶和车位来配置两大块。
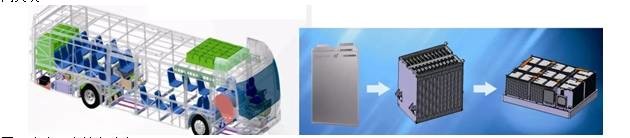
图5 上汽万向纯电动大巴
2) Navistar的HEV电池包
欧洲和美国也用了不少A123的电池系统(基础是20Ah的电芯),整个结构是非常类似的。如图6所示,采取单体串联=》模组并联=》再串联的电池构成的模式来获取大的容量。
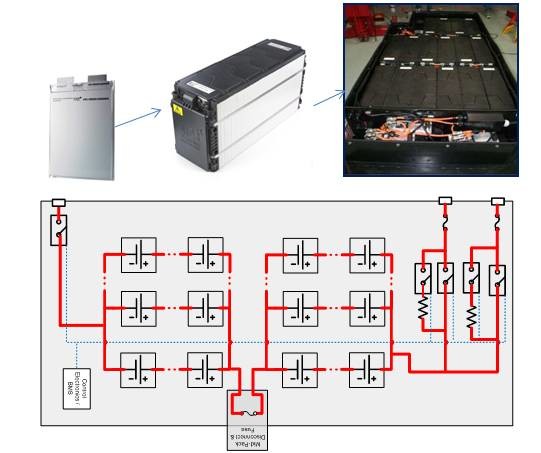
图6 Navistar的HEV大巴
总体来说,纯电大巴的电池系统结构,大体根据结构工程师来布置,分成4~8个包;HEV+PHEV的包呢,分的数量少一些都包在一起。区别的地方在于,如比亚迪和CATL(这两家)采取的是较大的单体,先串联然后总的进行并联配置,如比亚迪的系统设计。三组电池包并联,标准输出电压直流540V,组内电池模组串联,每组电池包21个模组,每个模组内含有8个单体电池(标准电压3.3V),模组的电压为26.67V。在K9的布置中,采取前桥承载1个电池包,后桥左右各承载一个电池包,整车高压线束通过左风道、车内电子路牌和右侧尾部立柱的模式,由于采取这种模式,比亚迪需要在每个电池包内进行配电管理,考虑主正、主负和预充继电器,每个电池包内需要一个BMS主控进行独立核算。
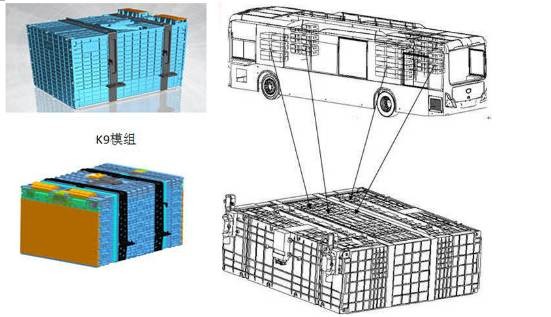
图7 比亚迪系统的设计
CATL的纯电动巴士通用电池箱230/320KWH,电芯:200Ah LFP(多层卷绕方形铝壳),模组为2P3S 或 3P2S,电池箱(铝压铸)为2P18S 或 3P12S(6个模组),电箱参数: 57.6V/23kWh 或 38.4V/23kWh;其中230kWh电池系统由10个2P18S电池箱串联,320kWh电池系统由14个3P12S电池箱串联。
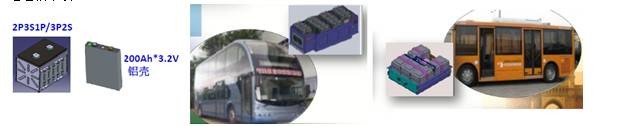
图8 CATL的系统设计
图9,是以前在分析五洲龙和沃特玛电池时候画的,算是比较典型的系统架构图,这里拿来作为完全串联的一种架构模式。
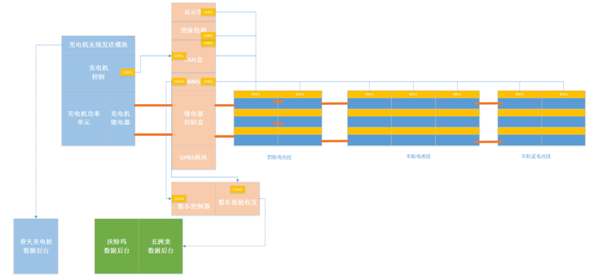
图9 沃特玛五洲龙的系统设计
所有大的新能源大巴这里的几个问题其实是普遍存在的:
1)单体确实比较大,采用LFP还是必由之路,否则200Ah的电芯,内层发热散热问题较大
2)电池包分别布置在多个区域,导致区域内的各种环境条件(温度、振动),整个电池组内的温差,按照实际的情况在10度以上
3)单个包,配置BMU或者继电器之后,本身的安全性需要独立设计核算,内部加继电器的,BMU的控制权限需要提升,整个分布式控制系统的低压控制线和通信线所受的回路比较大
4)电池模组的堆叠,机械应力上差异也比较大,把模组堆在模组上,其实不是好好的主意
第三部分 新能源大巴的BMS
新能源大巴几乎都是采用,分布式管理系统(电池管理系统+多个温度电压测量单元方式)将电池模组的功能独立分离,整个系统形成了单体电压和温度测量均衡单元、电池管理控制器、继电器控制器和整车控制器,三层两个网络的形式。这里主要考虑的问题还是基于模块化的考虑,生产和组装分离,在装车的时候进行网络配置。
如果单从BMS的角度来看,大巴车的BMS系统与乘用车的主要有以下的差异:
1) 由于大巴车辆的电源系统是基于24V系统,所以对于BMS来说里面需要考虑的供电问题。
a. 电源系统的特别是抑制这块需要单独设计,由于BMS的电源部分需要用个Buck电路来替代LDO,如图10所示,24V系统的考量还是需要在电源上做更多处理,否则脉冲抑制不住会烧毁器件。
b. 由于24V系统的原因,配置DC-DC是必须的,BMS的计算量偏大,总线频率和电流量就大一些,这里一般配置2路Buck拓扑的DC-DC给电源供电。
c.BMU的供电也是一个大问题了,所以BMU的内部架构,往往是只能将MCU、测量和备份芯片从模组取电,否则需要在BMS里面构建一个24V配电盒的功能,加些熔丝在里面了。
d. 由于大巴的24V电池容量高一些,对于漏电流方面的管理需要弱化一些。
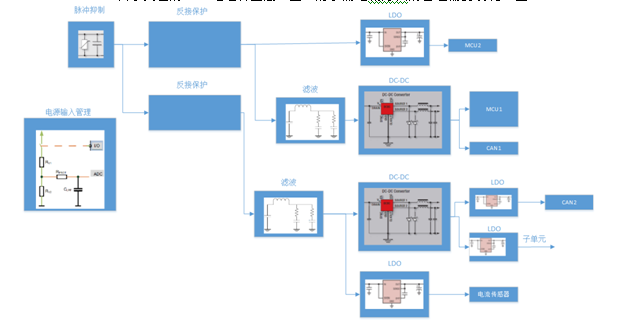
图10 BMS电源系统架构
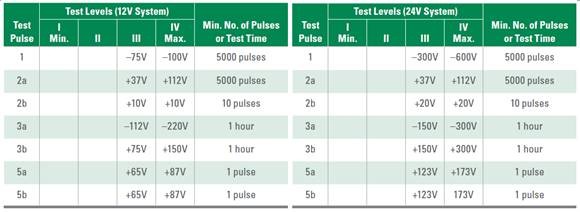
图11 12V和24V电源抑制
2) CAN通信的脉冲抑制,同上由于线束的布置问题,CAN上面的串扰不是一点点大,导致原有的设计需要更改。
a. BMS在这里一般有三路CAN电路,分诊断CAN、与整车控制器通信CAN和BMU的CAN,由于电池包的分散布置,使得整个BMS和BMU之间CAN的环路太长,耦合进来的东西会比较多。
b. 由于某些部件,比如电动压缩机、电机控制器,本身控制板上的CAN线耦合了很多的东西,使得BMS外部收到的干扰也很多,所以实际沟通下来的情况,就是通信电路和错误帧非常多。
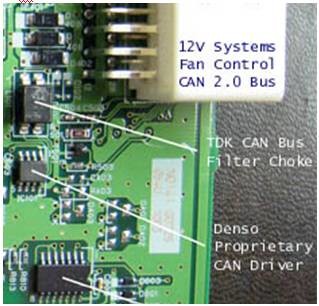
图12 乘用车CAN通信电路
3) 单体均衡,由于电动大巴容量(1个就是200Ah,还有2P和3P的)很大,很多公司用了加大的被动均衡或者主动均衡电路,这块区别也比较大,所以看到有公司给大的均衡电阻配置独立的散热器的。所以未来如果发展的方向是大容量的电池,像比亚迪这样提高母线的电压,将压力从单体容量上转移给逆变器和电机,就是IGBT上还是靠谱的。
4) 由于大巴的电源波动,某些公司甚至独立配了个12V备份电源独立给电池包内配置一个供电系统,所以一般BMU和BMS之间只有CAN线和报警线之间的关系了,这里补一个安全气囊的PWM报警输出口的电路,我个人觉得其实BMU和BMS之间在未来需要有一个额外的通信备份接口,用PWM定义确实比较合适,在图里面把Collision改成单体过压和模组过压的报警就可以直接使用了。
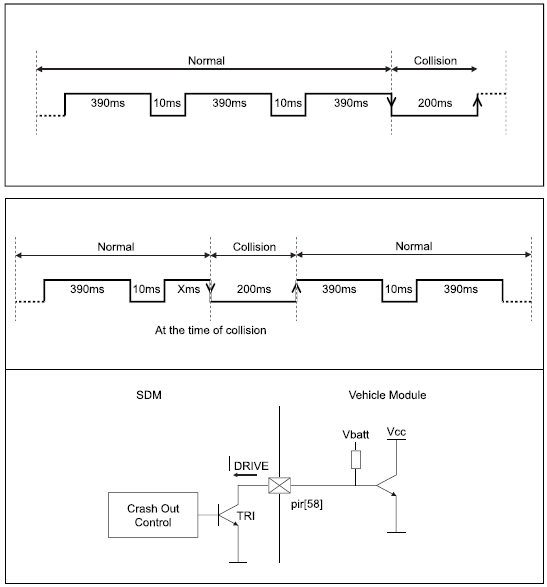
图13 PWM报警接口定义参考
这块内容,主要还是根据和汽车电子俱乐部的相关工程师一起交流和总结的内容,实际的情况比这个更复杂一些。由于大巴企业的BMS供应商普遍仅仅参考《QCT 897-2011 电动汽车用电池管理系统技术条件》这份行业标准来做产品,整个BMS产品的水平就很值得商榷了。如果仔细对比整个细节的参数和样品验证的数量,其实和GBT 28046-2011 道路车辆 电气及电子设备的环境条件和试验(1~5)之间都有很大的差距。
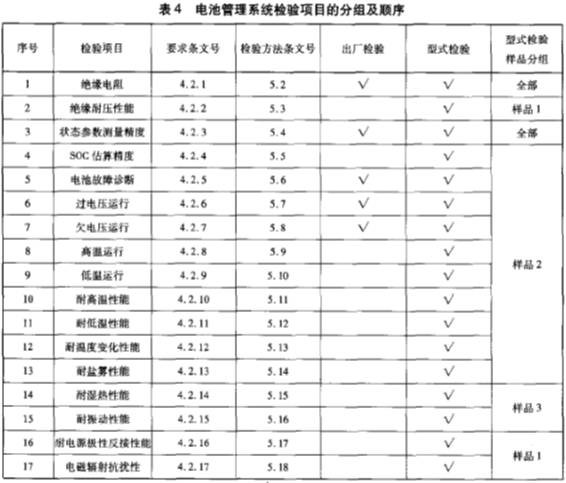
图14 QCT897-2011内技术要求
本文来源:电动汽车线束